When Italian-born Pasquale Zappia and his wife Mayra opened Via Oliveto in Toronto in 1988, the business was a combination restaurant/bakery serving area hotels, restaurants and caterers. A baker by trade, Pasquale handled the bakery. His wife ran the restaurant, followed by their sons Patrick and Adriano when they were old enough. Pasquale had always put his own spin on Italian breadmaking, but when he began baking crispy artisanal flatbread crackers – essentially a European-style flatbread cracker – he truly found his niche.
As demand for the triangular flatbread spiked among their food service customers, it became Pasquale’s sole focus. In 2006, the family sold the restaurant, and the sons joined their father in the bakery as it relocated to a 2,000 square-foot facility in Toronto. In 2007, they started packaging the product for retail sales in a few local food shops and “Pasquale’s Glorious Flatbread” was born. Soon it was also selling in area supermarkets, and by 2009 Via Oliveto moved into an 8,000 square foot location in Vaughan, just north of Toronto.
The manual production process
To produce the flatbread, the family evolved a unique, labor-intensive process involving convection baking in rack ovens. Their 24” wide system included a bowl mixer, a three-roll sheeter, three gauge rolls and 18” by 26” pans. Semi-automatic equipment sprayed the cut triangular pieces of dough with water, salt, seeds and herbs before the trays were manually placed into the rack ovens to bake, then manually removed to cool. This process included four double rack ovens with 32 aluminum racks and 2,500 baking pans, all of it handled by four people.
Production on this system peaked at about 100 kg per hour, and it made growing the bakery a challenge. The Zappias knew they wanted to upgrade to a more automated, labor-saving solution, they just didn’t know how, or if it was even possible.
The family began reaching out to oven manufacturers in 2019. Their efforts included a trip to the International Baking Industry Exposition (IBIE) in Las Vegas, where they met more oven manufacturers and got system quotes. Some of those OEMs didn’t quite understand what the Zappias needed, and others proposed oven systems that were either too big, or too expensive. But luckily, also found their way to the RBS booth.
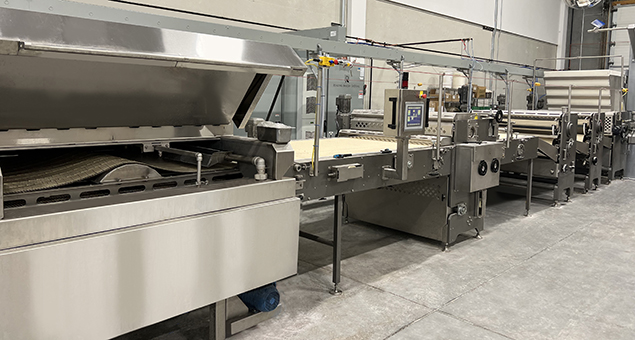
Meeting RBS at IBIE
The Zappias were struck by how confident RBS was that they could help Via Oliveto move from rack ovens to a tunnel oven system. “We thought, how could this be so easy for them?” recalls Patrick Zappia. “We thought it was going to be such a challenge – but no, RBS made it sound like the opposite.” The family was impressed by the company’s willingness to work with such a small bakery. They also liked that RBS was proposing a one-stop-shop solution that featured an integrated sheeting line and oven, with flexibility for other products in the future.
R&D product trial success at RBS
In January 2020, Pasquale, Patrick and Adriano drove to the RBS Science & Innovation Center to see how the Multi-Crisp System would handle their five flatbread varieties. The Zappias wanted to be sure that the final products would be similar enough to what they were already producing that their customers wouldn’t notice any difference.
RBS successfully created all the flatbread recipes on the first trial day. In fact, the Multi-Crisp System actually improved product quality. By eliminating the hot and cold spots the family faced with their rack ovens, the RBS system delivered a more even baking process that gave the flatbread a better mouthfeel.
After seeing and tasting the successful results, the Zappias were convinced that going with RBS was the right decision. Within a few months, Via Oliveto and RBS closed the deal, even as COVID-19 quarantines were in full swing.
System installation and setup
RBS installed the new Multi-Crisp System in September 2021. The system uses a non-RBS mixing bowl, as the Zappias wanted to upgrade to a larger model of the same mixing bowl they were already comfortable with. The bowl mixes 200 kg batches of dough at a time, which a bowl elevator then dumps into a hopper that feeds into a 3-roll sheeter, two gauge rolls, then a rotary cutter with two die rolls.
Next, the cut dough moves on a conveyor into a caustic cooker, where it is doused with pressurized water before RBS Omega topping dispensers distribute salt, seeds or herbs as each recipe requires. The dough pieces then travel into a 48” wide SPECTRUM OVEN® with two baking zones and an open weave baking mesh.
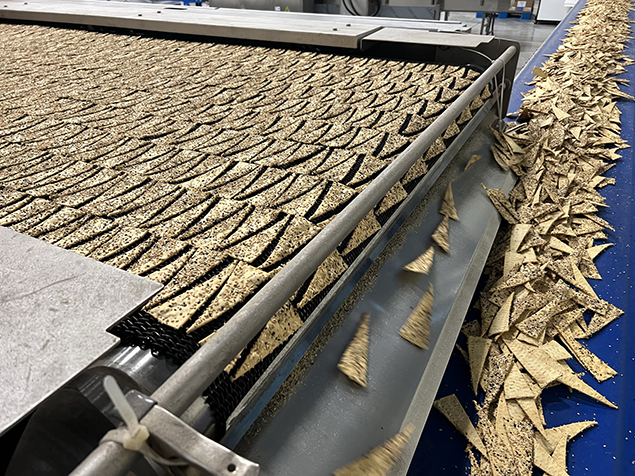
Via Oliveto today and tomorrow
At the time of this writing, Patrick and Adriano have been running the Multi-Crisp System for about 15 months. Flatbread production has quadrupled to 400 kg per hour, and the brothers are setting their sights on a long-term goal of 600 kg. What used to require three to four people can now be accomplished with “one-and-a-half to two,” notes Patrick.
As Patrick explains, “We don’t have to worry about opening oven doors, checking on the product, adding baking time, closing oven doors – the oven part of our production is now 100% hands-off, so we can really focus on the things that affect recipe quality.”
The flexible Multi-Crisp System has also allowed them to start baking a “pretzelized” version of their flatbread, or as Patrick calls it, “a European-style artisan pretzel.” Currently the Zappias produce the pretzel for private label sales but soon intend to offer them to the Canadian and US supermarkets now stocking their flatbread.
So, what closing words of advice does Patrick have for other small bakeries thinking about working with RBS? “Do it! Throughout this whole process I always felt like we’ve been listened to and that we were working with a company who’s going to do everything they can to make us a success.”