CAMP HILL, PA. — It was 2021 when automation was highlighted as a corporate-wide priority by ADM’s chief executive officer Juan Luciano. For the company’s flour milling business, the ambition to automate has become a greater reality with the comprehensive modernization at the ADM flour mill in Camp Hill, Pa.
Cady Roberts, commercial director of ADM’s milling business, said automation and modernization of the aging B mill at Camp Hill last year were but two of numerous formidable goals the company set, doggedly pursued and successfully achieved in completing the project.
With the first major milling capital project since the business moved its sales and commercial office to Decatur, Ill., in 2019 from its longtime home in Overland Park, Kan., ADM was keen on tapping into deep internal corporate resources to draft and execute the best possible plan for the mill, Ms. Roberts said. Toward that end, ADM leaned into another initiative from the start of the 2020s — the creation by ADM of centers of excellence (COEs) in procurement, supply chain and operations.
Capacity of the B mill was left unchanged from before the 2022 project, leaving Camp Hill with 12,500 cwts of daily milling capacity, split between 7,500 cwts for the A mill (mostly a hard wheat mill) and 5,000 cwts for the B mill. Served by the Norfolk Southern railroad, the mill has 998,000 bus of grain storage capacity. The complex also features a warehouse and bulk storage totaling approximately 37,500 cwts of flour.
The B mill project was scheduled to be executed on a tight timeline — eight months from start to finish — while the A mill continued to operate. Built more than 70 years ago, the B mill was not among the easier of ADM’s 250 plants around the world to choose to automate.
The project was launched early in 2022, while the COVID-19 pandemic was still causing business interruptions and late pandemic supply chain disruptions were peaking.
“Engaging our centers of excellence from procurement, safety, quality, automation, their roles, was a major leverage point for us and really made this project successful as well,” Ms. Roberts said.
The centers of excellence were established by ADM to connect experts in different topic areas with colleagues at the company to “accelerate productivity and innovation, keep our plants running, complete projects on time and within budget, and keep our people safe,” ADM said.
Capping off a job from 2022
Gabriella Huebner, ADM’s technology engineer who oversaw the project, said the approach to modernizing the B mill was different than building a new mill from the ground up or completely gutting an existing mill. ADM had installed in 2016 new Bühler sifters and upgraded the pneumatic system of the B mill and saw the 2022 project as “finishing the job.”
“With new mills, you design first and then build around it,” she said. “The B mill is sandwiched between different buildings, and we wanted to preserve the modernization, which runs really well, and we were limited by the existing building structure. It meant we couldn’t radically change the mill flow.”
Rather than use a single vendor to design the mill update and supply all or nearly all the equipment, an ADM team headed by Ms. Huebner oversaw the redesign and selected the equipment from a range of allied suppliers.
The mill’s equipment is spread across five floors with lower ceilings than are typical in mills built over the last few decades but was common in the early and mid-20th century. The mill’s roll stands had been installed on two floors. Three line shafts powered the roll stands on the mills first floor with four individual powered roll stands on the second floor.
“The main scope of this project was to take out our three line-shaft driven roll stands, do all new electrical, all new instrumentation and all new automation with new Ugur roll stands that are in there today,” Ms. Huebner said.
For the update, roll stands were consolidated onto a single floor (the first floor) resulting in a reduction of roll surface area compensated for with other milling equipment. Spouting and other equipment was moved to enhance mobility for mill personnel.
“It’s a much cleaner system,” Ms. Huebner said. “Spouting has been positioned to safely allow easier access and exit.”
In the basement, which was cluttered before the modernization with large motors and concrete bases on the ground, the three line shafts were removed and motors were installed on the ceiling.
Aesthetically, the basement now has the “bright modern look most mills have,” Ms. Huebner said.
Fewer roll stands
One Bühler and five Kice bran detachers were installed in the basement. The detachers and Kice bran dusters on the second and fourth floor help maximize extraction, preserving the mill’s rated storage capacity despite the reduction in roller mills.
Only a few structural changes to the building were made. A wall needed to be taken apart to expand a utility closet into a control room (the B mill previously had no control room). After the old roll stands were removed in February, the wood floors were pulled up from the first and second floors, structural steel supports were installed to hold the heavier load of new equipment, and double-thick marine-grade plywood was laid and epoxy applied to seal it.
The new roll stands were installed on the first floor while a few existing conveyors, still in good condition, were moved from the first floor to the second. The rest of conveyance was all new from EBM. The roll stands were in place by May. The control room was completed in September.
On the second floor, conveyors were installed and spouting was put in place in June and July. The spouting was configured to minimize angles and maximize flow as well as mobility across the floor.
“A lot of the spouting before the conveyors — were at shallow angles,” Ms. Huebner said. “The shallower it is, the harder it is to maintain that flow and the more susceptible you are to chokes. It had been a little chaotic to get things done on the second floor.”
The new Kice bran dusters were added as well, replacing outdated models, Ms. Huebner said.
“It challenged us a lot,” she said. “There are a lot of conveyors and other equipment on the second floor. The floor showcases the benefits of doing the project on our own and not using a big vendor. We were able to choose our own equipment, what would work best at this facility.”
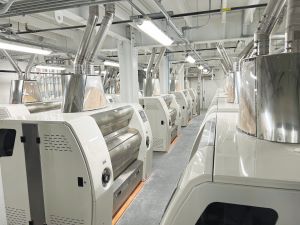
Ms. Roberts added, “It’s a more tailored approach rather than a one size fits all.”
As a result, it was “Definitely a lot more work for us,” Ms. Huebner added.
She said Camp Hill benefited from learnings gained in other recent projects.
“We repeatedly talked to the technology and operations people,” she said. “We had done Mendota (Ill.). We had done Enid (Okla.). We definitely tapped into them to select the best equipment, that worked best.”
Updates were more modest on the third and fourth floors. Changes included the installation of scales made by Swisca AG and cosmetic touch ups, including painting and applying epoxy on the floor.
Flour valves were installed on the second floor giving mill operatives easy access to flour samples to ensure the mill is running well. In the past, millers would need to access samples from beneath sifters, which was neither convenient nor as safe, Ms. Huebner.
New Bühler filters, airlocks and cyclones installed in 2016 on the fourth floor were left in place. Changes on the floor in 2022 included moving flour dusters to the fourth floor as well as additional Swisca scales and replacing the second-floor dusters with four newer model Kice models on the second floor.
Other technology needed updating as well. The mill’s electric panel sat exposed in an old warehouse, a separate building, meaning operatives would need to leave the mill to access the control panel.
“The warehouse was very inconvenient,” said Drew Stewart, plant manager.
The electrical update was dramatic, a necessary change to make the automation possible, Ms. Huebner said.
New smart MCCs (motor control centers) were installed as were all new sensors. The change gives operatives local disconnect and an e-stop (emergency stop) buttons. Electronics are connected through an ethernet system.
“There are new sensors on everything,” Ms. Huebner said. “It will tell you if it chokes. It will tell you if it’s not moving. Now we have local disconnects on every piece of machinery.”
The change allows the mill to be started up or shut down in only a few minutes, a process that easily took 30 minutes in the past.
No ‘out-of-the-box’ solution
More generally, automation at Camp Hill is not an “out-of-the-box” solution, Ms. Roberts said. Tapping the resources of ADM’s automation COE, a base system is tailored to the needs of each individual facility, she said. She noted the approach allows for in-house support from ADM’s automation information technology department, versus using a contractor.
“No matter if you’re oilseeds, corn or wheat milling, we all are in some ways measuring the same data points — yields and outputs,” she said. “We really leveraged that base knowledge and subject matter experts to tailor this. We also pulled in our head millers. Drew had a lot of experience, polling other facilities what they had experienced at their facilities as we planned the automation system with the idea of replicating those experiences. The system was tweaked during commissioning based on feedback from the millers.”
Mr. Stewart said the millers were asked collectively what information was most important to display front and center.
“For me, the center screen ‘must have’ was roll motor amp information,” he said. “A one-stop place so you know what your rolls are doing.”
Ms. Huebner added, “Trend data was a big deal, too. Trends for scales show whether final output is gaining or losing. We added them for different machines.”
HMI (human machine interface) monitors help communicate key data on each floor, flagging problems when they emerge.
Scales provide both instant mill rates and trends as well as downtime coding and facilitates downtime communication between shifts.
“Importantly, there’s lots of troubleshooting for root cause analysis,” Ms. Huebner said. “It’s instant, so if you’re on the fourth floor and something goes down, the automation system will say, ‘Hey, on the second floor a choke sensor went off.’ You can go right to the problem.”
With the installation of fail-safe sensors, key equipment will remain shut off until it is fixed.
“It keeps the mill reliable and safe,” Mr. Stewart said. “It’s particularly reassuring if a miller goes into the A mill knowing the B mill would shut down promptly if a problem arises.”
While the company touts having a large constellation of flour mills as a way to ensure customers of its dependability as a supplier, ADM also is investing to ensure each of its mills individually is as reliable as possible, Mr. Stewart said. For example, vibration monitors have been installed to ensure motor bearings and fan shaft bearings are operating as they should and at the correct temperature.
“It’s one of the company’s big pushes — predictive maintenance,” Mr. Stewart said. “One of the ADM centers of excellence is maintenance and reliability, and that’s something we’re really working toward.”
Ms. Roberts added, “Troubleshooting is more proactive when it was reactive before.”
The improvements gleaned from upgrading the mill’s equipment involve other key metrics of the mill’s performance.
“We’ve seen a 3 to 5 percentage-point improvement in our extraction,” Mr. Stewart said. “We’ve seen our ash curve shift, so we are able to run a higher percentage at a lower ash, making more of the quality flour. Those are two enormous benefits.”
In addition to improved extraction, Ms. Roberts said the mill had struggled in recent years to produce at its rated capacity of 5,000 cwts per day.
“Now it’s very easy,” she said.
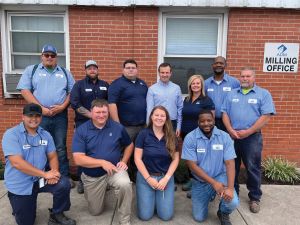
Source: ADM
Replacing obsolete roll stands was a key to the improvement, Ms. Huebner said. The Camp Hill mills are staffed efficiently with a total of two operatives per shift — a head miller and an assistant miller.
“Before the 2022 project, the operators had to constantly adjust those roll stands to be sure they were holding their grind,” she said. “They just didn’t hold. It would back off or tighten too much. Now they have these new roll stands that hold the grind all shift long.
“They are spending less time finagling stuff. It’s easier to run two mills at once when you can rely on the equipment.”
While in the past, the mill would depend on operators of the bulk storage facility for their blending expertise to ensure all flour met customer specifications, sometimes correcting problems, the mill now generates needed flour consistently, Ms. Huebner said.
“Our blenders and bulk loaders make us more efficient through the whole process, and product is ready to go right off the mill,” Ms. Roberts said.
To complete the project while the pandemic was still in a disruptive phase, and while the A mill was still running amid the tightest supply chain in memory, was no small feat, Ms. Huebner said. Over 20,000 hours of contractor work was logged on the project, 25,000 hours including work completed by ADM team members, all without a safety incident.
“They were working quickly, in tight spaces,” she said. “That was lots of people working on top of one another, and they all went home safely.
“And we were still a working mill while the B mill was shut down. We still had the A mill, we were still packing, unloading bulk wheat, loading bulk trucks.”
Thoroughly vetted suppliers
Ms. Huebner and Mr. Stewart highlighted features of the Swisca AG scales installed at the Camp Hill mill.
The interchangeability of Swisca spare parts represents a major advantage, Ms. Huebner said.
“They’re also servo driven rather than air actuated,” Mr. Stewart said. “Your servo motor either works or fails. With air, if you have air pressure issues or water in your air line, that causes problems with the scales.”
Well before selecting the Ugur roll stands for Camp Hill, ADM purchased a couple others and installed them at other plants.
“The Ugurs have been very good roll stands,” Ms. Huebner said. “This is the first full scale mill installation, but the trial Ugurs had worked very well at our other plants.”
The trials helped establish that the roll stands were able to hold their grind, that the hopper systems and variable speeds on the rolls worked well.
“We’ve also had Swisca scales at other plants,” Ms. Huebner said. “We didn’t go into it blindly wondering whether they would work or trusting someone’s word. We knew they worked.”
While the Camp Hill property is not large enough to accommodate unit train unloading, John Sigler, commercial manager, said rail service has not been a problem.
“We maintain a good relationship with the local rail master here as well as the salesmen and the relevant employees at Norfolk Southern so we get good support,” he said.
Because flour sales are handled in Decatur, Mr. Sigler’s responsibilities broadly focus on meeting customer requirements.
“I make sure customers are getting deliveries on time, and that we’re well managed on the transportation side,” he said. “We have a diversified mix both of ADM trucks and outside carriers to deliver the flour. We use in-house supply-chain software to look at different data points on how we are delivering and make adjustments based on that data.”
Wheat buying responsibilities are divided between the local team and grain procurement professionals in Decatur.
“At the B mill we procure all the soft wheat locally within 100 miles,” Ms. Roberts said. “Hard wheats are railed in for the A mill. We have the capacity to swing the A mill to soft wheat, depending on customer demand.”
Going forward, Ms. Roberts said the Camp Hill project may be a model for what to expect in terms of ADM capital projects in flour milling.
“I think you will see us accelerate in more of the same areas as the B mill,” she said. “You will see more of that at some of our core flour facilities as we look to maintain or grow in various areas of the market. That’s more likely than greenfield projects. It’s about bringing automation to an older facility, without having to totally tear down.”